Inventory management system is crucial for efficient business operations. Effective inventory control directly impacts profitability, minimizing waste from overstocking and lost sales due to shortages. This guide explores the core components, implementation strategies, optimization techniques, and technological advancements within inventory management systems, providing a comprehensive understanding for businesses of all sizes.
From defining the various types of inventory management systems (perpetual vs. periodic) and their suitable applications, we’ll delve into key features like demand forecasting and the integration with other business systems, such as Point of Sale (POS) and accounting software. We’ll also cover crucial aspects like data management, security, and the use of technologies like barcode scanning and RFID to enhance accuracy and efficiency.
Defining Inventory Management Systems
Inventory management systems (IMS) are crucial for businesses of all sizes, providing a structured approach to tracking and managing stock levels. Efficient inventory management directly impacts profitability by minimizing waste, optimizing storage, and ensuring timely fulfillment of customer orders. A well-implemented system allows for better forecasting, reducing the risk of stockouts or overstocking.
Inventory management systems encompass several key components working in concert. These typically include database management for storing inventory data, order processing capabilities for managing incoming and outgoing goods, reporting and analytics tools for tracking key performance indicators (KPIs), and integration with other business systems such as accounting and sales platforms. The sophistication of these components varies depending on the chosen system and the business’s specific needs.
Types of Inventory Management Systems
Businesses employ different approaches to inventory management, each with its own advantages and disadvantages. Two primary methods are perpetual and periodic inventory systems. Perpetual systems maintain a continuous record of inventory levels, updating balances in real-time with each transaction. This offers greater visibility into stock levels but requires more robust tracking mechanisms. Periodic systems, on the other hand, involve physically counting inventory at fixed intervals, such as monthly or quarterly. This method is simpler to implement but provides less real-time data and a higher risk of inaccuracies. The choice between these systems often depends on factors such as the volume of inventory, the value of individual items, and the level of accuracy required.
Businesses Benefiting from Inventory Management Systems
A wide range of businesses can significantly benefit from implementing an inventory management system. Retailers, for example, can optimize shelf space and prevent stockouts of popular items, leading to increased sales and customer satisfaction. Manufacturers benefit from better control over raw materials and finished goods, reducing production delays and waste. E-commerce businesses rely on IMS to manage a large and diverse product catalog efficiently, ensuring timely order fulfillment and accurate shipping information. Restaurants and food service businesses can use inventory management to reduce food spoilage and optimize purchasing decisions. Essentially, any business that deals with significant quantities of goods or materials can gain from the improved efficiency and accuracy offered by a well-chosen inventory management system.
Comparison of Inventory Management Software Solutions, Inventory management system
Choosing the right inventory management software depends on a business’s specific requirements and budget. The following table compares three popular options, highlighting their key features and pricing models. Note that pricing can vary depending on the number of users and specific features selected.
Software | Key Features | Pricing Model | Integration Capabilities |
---|---|---|---|
Zoho Inventory | Order management, inventory tracking, reporting, multi-channel sales integration | Subscription-based, tiered pricing | Integrates with various e-commerce platforms and accounting software. |
Fishbowl Inventory | Manufacturing-focused features, barcode scanning, robust reporting, lot and serial number tracking | One-time purchase or subscription options | Integrates with QuickBooks and other accounting software. |
inFlow Inventory | User-friendly interface, customizable reports, barcode and RFID support, multi-location inventory tracking | Subscription-based, tiered pricing | Integrates with various e-commerce platforms and accounting software. |
Key Features and Functionality
Effective inventory management hinges on a robust system equipped with key features that streamline operations and optimize resource allocation. These features work in concert to provide real-time visibility into inventory levels, facilitating informed decision-making and minimizing waste. This section will delve into the core functionalities that define a successful inventory management system.
Demand Forecasting in Inventory Management
Demand forecasting plays a crucial role in preventing stockouts and minimizing excess inventory. Accurate predictions allow businesses to procure the right amount of goods at the right time, optimizing storage space and reducing carrying costs. Sophisticated forecasting models, incorporating historical sales data, seasonal trends, and market analysis, provide a more reliable estimate of future demand than simple extrapolation. For example, a retailer anticipating a surge in demand for winter coats during the colder months can use forecasting to adjust their orders accordingly, ensuring sufficient stock to meet customer needs without overstocking. This proactive approach minimizes potential losses from lost sales or excessive storage fees.
Accurate Inventory Tracking and its Impact on Business Operations
Precise inventory tracking is fundamental to efficient operations. Real-time visibility into stock levels prevents stockouts, reduces order fulfillment times, and minimizes the risk of obsolescence. Automated tracking systems, using barcode scanners or RFID technology, ensure data accuracy and eliminate manual errors, providing a more reliable basis for decision-making. For instance, a manufacturing company using real-time inventory tracking can immediately identify a shortage of a critical component, enabling prompt action to avoid production delays and potential revenue loss. The resulting improvement in operational efficiency translates directly to increased profitability.
Benefits of Integrating Inventory Management with Other Business Systems
Integrating inventory management with other business systems, such as Point of Sale (POS) systems and accounting software, creates a seamless flow of information and enhances operational efficiency. A POS system integrated with inventory management automatically updates stock levels after each sale, providing an accurate real-time inventory count. Similarly, integration with accounting software streamlines financial reporting, automating the tracking of inventory costs and providing valuable insights into profitability. This integrated approach eliminates data silos, minimizes manual data entry, and reduces the risk of errors. For example, a restaurant using integrated systems can automatically track ingredient usage, facilitating accurate cost accounting and optimizing ordering processes.
Inventory Management Process Flowchart
The following describes a typical inventory management process flow:
The process begins with Receiving inventory. This involves verifying the quantity and quality of goods received against the purchase order. Next, the inventory is Stored in designated areas, often organized using a specific system (e.g., FIFO, LIFO). Finally, inventory is Distributed based on demand, whether it’s fulfilling customer orders or supplying internal production needs. The system then updates inventory levels to reflect the movement of goods. This cyclical process ensures a constant flow of goods while maintaining accurate inventory records.
Efficient inventory management is crucial for any business, ensuring optimal stock levels and minimizing waste. However, scaling this efficiency during rapid growth requires a robust strategy, which is where a well-defined framework like the Rapid growth framework can prove invaluable. By implementing such a framework, businesses can proactively manage their inventory systems to keep pace with increased demand and maintain profitability.
Imagine a simple diagram: A box labeled “Receiving” leads to a box labeled “Storage,” which in turn connects to a box labeled “Distribution.” Arrows indicate the flow between these stages. Each box could contain further sub-processes such as quality checks (Receiving), stock location assignment (Storage), and order fulfillment (Distribution). Feedback loops could show the updating of inventory levels after each stage.
Efficient inventory management systems are crucial for any business, ensuring optimal stock levels and minimizing waste. Understanding logistics is key, and this often involves efficient transportation; for helpful guidance on navigating public transport options, check out this guide: Panduan menggunakan transportasi umum. Returning to inventory, timely delivery, facilitated by understanding transportation networks, directly impacts the accuracy and effectiveness of your inventory system.
Implementing an Inventory Management System
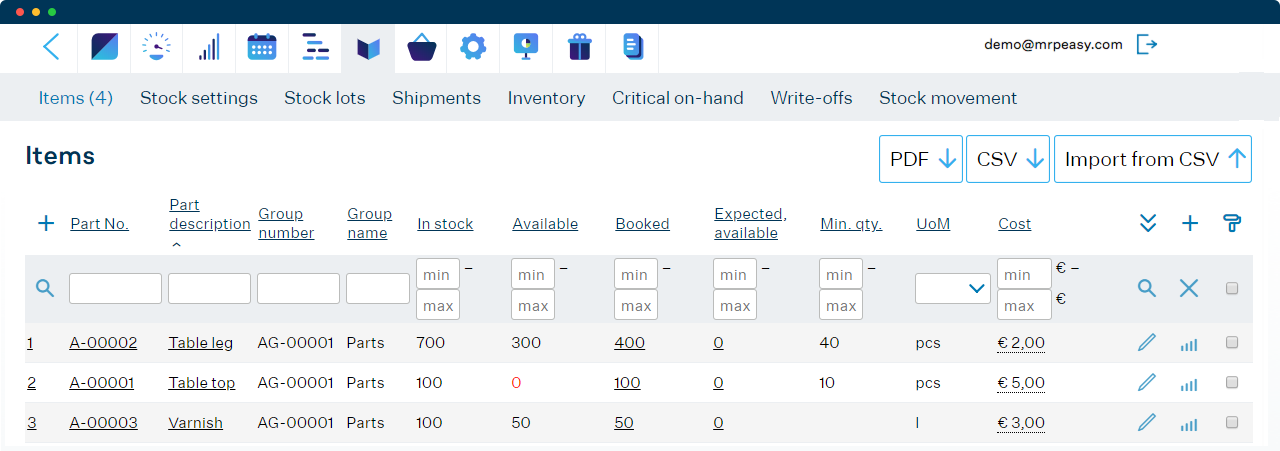
Implementing a new inventory management system (IMS) can significantly streamline operations and improve efficiency. However, a successful implementation requires careful planning and execution. This section details best practices for selection, implementation, data migration, and addresses potential challenges.
Best Practices for Selecting and Implementing an Inventory Management System
Choosing the right IMS is crucial. Consider factors such as the system’s scalability to accommodate future growth, its integration capabilities with existing software (like accounting or CRM systems), and its user-friendliness for your team. Thorough vendor research, including requesting demos and reading reviews, is essential. Implementation should involve a phased approach, starting with a pilot program in a small area before a full rollout. This allows for adjustments and reduces the risk of widespread disruption. Robust training for all users is also paramount to ensure system adoption and proficiency.
Data Migration from an Existing System to a New One
Migrating data from an old system to a new one is a critical and often complex step. Begin by thoroughly cleaning and validating your existing data to eliminate inconsistencies and errors. This process might involve data scrubbing, deduplication, and standardization. Next, develop a detailed migration plan, outlining the steps, timelines, and responsibilities. This plan should also specify how data will be transformed to fit the new system’s structure. Consider using a phased approach for data migration, migrating smaller subsets of data first to test the process and identify any issues before migrating the entire dataset. Post-migration, rigorous data validation is crucial to ensure data integrity and accuracy.
Potential Implementation Challenges and Mitigation Strategies
Several challenges can arise during IMS implementation. One common issue is resistance to change from employees accustomed to the old system. To mitigate this, provide comprehensive training and clearly communicate the benefits of the new system. Another challenge is data integration issues, particularly when connecting to legacy systems. This can be addressed by ensuring compatibility between systems and employing robust data mapping and transformation techniques. Unexpected system downtime or technical glitches can also occur; having a contingency plan, including backups and disaster recovery procedures, is crucial. Finally, insufficient user training can lead to low adoption rates and hinder the system’s effectiveness; comprehensive, hands-on training programs are essential.
Configuring Inventory Management System Settings
Configuring settings like reorder points and safety stock levels is vital for optimal inventory management. Reorder points are calculated using factors such as lead time (the time it takes to receive an order), average daily demand, and safety stock. A common formula is:
Reorder Point = (Lead Time Demand) + Safety Stock
. Safety stock acts as a buffer against unexpected demand fluctuations or delays in delivery. The appropriate safety stock level depends on factors like demand variability and the cost of stockouts. These settings should be regularly reviewed and adjusted based on historical data and current market conditions. For example, a company experiencing seasonal demand fluctuations might increase safety stock levels during peak seasons and decrease them during slower periods.
Inventory Optimization Techniques: Inventory Management System
Effective inventory management is crucial for profitability. Optimizing inventory levels requires a strategic approach, balancing the costs of holding excess stock against the risks of stockouts. This involves understanding various inventory control methods and employing techniques to minimize costs while ensuring sufficient supply to meet demand.
Inventory Control Methods: FIFO, LIFO, and Weighted Average
Different inventory costing methods impact the valuation of goods and the calculation of cost of goods sold. First-In, First-Out (FIFO), Last-In, First-Out (LIFO), and Weighted Average Cost methods each offer a unique approach to tracking inventory flow and value. FIFO assumes that the oldest items are sold first, resulting in a cost of goods sold reflecting older purchase prices. LIFO, conversely, assumes the newest items are sold first, reflecting current prices in the cost of goods sold. The weighted average cost method calculates the average cost of all items in inventory and uses this average to determine the cost of goods sold. The choice of method can significantly influence financial statements and tax liabilities. For example, during periods of inflation, LIFO will generally result in a higher cost of goods sold and lower net income compared to FIFO.
Optimal Order Quantity Calculations
Determining the optimal order quantity (EOQ) is vital for minimizing inventory holding and ordering costs. The Economic Order Quantity (EOQ) formula helps businesses find the ideal order size to balance these costs. A common formula is:
EOQ = √[(2DS)/H]
Where:
* D = Annual demand
* S = Ordering cost per order
* H = Holding cost per unit per year
For instance, if a company has an annual demand (D) of 10,000 units, an ordering cost (S) of $50 per order, and a holding cost (H) of $2 per unit per year, the EOQ would be:
EOQ = √[(2 * 10,000 * $50) / $2] = 707 units
This suggests that ordering 707 units at a time would minimize the total inventory costs. Other models, such as the Economic Production Quantity (EPQ), are used when production is continuous rather than instantaneous.
Lead Times and Variability’s Impact on Inventory Levels
Lead time, the time between placing an order and receiving it, significantly impacts inventory levels. Longer lead times necessitate higher safety stock to buffer against potential delays and demand fluctuations. Variability in lead times and demand further complicates inventory management. Increased variability requires a larger safety stock to maintain a desired service level, which directly increases holding costs. For example, a company experiencing unpredictable customer demand might maintain a larger safety stock to avoid stockouts, even if it increases overall inventory costs.
Strategies for Reducing Inventory Holding Costs
Effective inventory management strategies are crucial for minimizing holding costs. These costs encompass storage, insurance, taxes, obsolescence, and the opportunity cost of capital tied up in inventory.
- Implement robust demand forecasting techniques to accurately predict future demand and optimize ordering quantities.
- Improve inventory tracking and visibility using technology like barcode scanners and RFID tags.
- Negotiate better terms with suppliers to reduce ordering costs and lead times.
- Optimize warehouse layout and processes to improve efficiency and reduce storage costs.
- Implement just-in-time (JIT) inventory management to minimize holding costs by receiving materials only when needed.
- Regularly review and adjust inventory levels based on sales data and market trends.
- Consider implementing inventory control software to automate tasks and provide real-time insights.
Reporting and Analysis
Effective inventory management relies heavily on the ability to track key performance indicators (KPIs) and analyze the resulting data. Inventory management systems provide this capability through a range of reports that offer insights into stock levels, sales trends, and overall operational efficiency. These reports are crucial for informed decision-making, allowing businesses to optimize their inventory strategies and minimize costs.
Inventory management systems generate reports by collecting and processing data from various sources, including sales transactions, purchase orders, and stock movements. This data is then used to calculate KPIs and generate reports that visualize key aspects of inventory performance. The system’s reporting capabilities allow for a deeper understanding of inventory dynamics, enabling proactive adjustments to inventory levels and strategies.
Essential Inventory Management Reports
Several key reports provide critical insights for effective inventory management. These reports offer a comprehensive overview of inventory status, sales performance, and potential areas for improvement. Analyzing these reports regularly allows businesses to identify and address inefficiencies, ultimately leading to cost savings and improved profitability.
Stock Status Reports
Stock status reports provide a real-time overview of the current inventory levels for each item. These reports typically include information such as the quantity on hand, the reorder point, and the lead time for replenishment. This information is vital for preventing stockouts and ensuring sufficient inventory to meet customer demand. A well-designed stock status report can easily highlight items nearing their reorder point, allowing for timely procurement actions.
Sales Reports
Sales reports track the sales performance of individual items or product categories over a specified period. This information is essential for forecasting future demand and optimizing inventory levels. By analyzing sales trends, businesses can identify popular items, slow-moving items, and seasonal variations in demand. This data can then be used to adjust purchasing strategies and prevent overstocking or stockouts.
Sample Reports
The following tables illustrate examples of stock status and sales reports generated by an inventory management system. These are simplified examples, and actual reports may contain more detailed information depending on the specific system and business needs.
Sample Stock Status Report
Item ID | Item Name | Quantity on Hand | Reorder Point | Lead Time (days) |
---|---|---|---|---|
12345 | Widget A | 100 | 50 | 10 |
67890 | Widget B | 25 | 30 | 5 |
Sample Sales Report
Item ID | Item Name | Units Sold (Last Month) | Revenue (Last Month) |
---|---|---|---|
12345 | Widget A | 80 | $8000 |
67890 | Widget B | 15 | $750 |
Data Analysis for Improved Decision-Making
Analyzing data from inventory management reports allows businesses to make informed decisions about various aspects of their operations. For example, identifying slow-moving items can lead to strategies like discounting or promotional offers to accelerate sales. Conversely, consistently high-demand items might indicate the need for increased procurement or alternative sourcing options to prevent stockouts. Predictive analytics, based on historical sales data and seasonal trends, can further enhance forecasting accuracy, allowing for more precise inventory planning and reduced waste. A retail chain, for instance, might use sales data from previous holiday seasons to predict demand for specific items and optimize stocking levels accordingly, minimizing losses from unsold inventory and ensuring sufficient stock to meet peak demand.
Technology and Integration
Effective inventory management relies heavily on integrating the right technology. Modern systems leverage various technological advancements to streamline processes, improve accuracy, and enhance overall efficiency. This section explores the key technologies and their integration within inventory management systems.
Barcode Scanning and RFID Technology
Barcode scanning and Radio-Frequency Identification (RFID) are crucial technologies for automating data capture in inventory management. Barcode scanners read linear barcodes printed on product labels, providing quick identification for tracking and updating inventory levels. RFID, on the other hand, uses radio waves to identify and track tagged items without line-of-sight, allowing for faster and more accurate inventory counts, especially in large warehouses or with fast-moving items. RFID offers advantages over barcodes in high-volume settings due to its ability to read multiple tags simultaneously. For example, a retail store could use RFID tags on clothing items to track inventory in real-time, instantly knowing stock levels on the sales floor and in the backroom, minimizing stockouts and optimizing shelf space.
Cloud-Based Inventory Management Systems
Cloud-based inventory management systems offer numerous advantages over on-premise solutions. Accessibility from anywhere with an internet connection is a major benefit, allowing authorized personnel to access and update inventory data remotely. Scalability is another key advantage; cloud systems can easily adapt to changing business needs, accommodating growth without requiring significant upfront investment in hardware or software upgrades. Furthermore, cloud providers typically handle data backups and security, reducing the burden on the business. For instance, a small business could start with a basic cloud-based system and easily scale up as its operations expand, adding features and user accounts as needed without the need for expensive IT infrastructure. Reduced IT costs and automatic software updates are also key benefits of cloud-based solutions.
Integration with E-commerce Platforms
Seamless integration between inventory management systems and e-commerce platforms is essential for efficient online retail operations. This integration ensures that online inventory levels accurately reflect real-time stock, preventing overselling and order fulfillment issues. Data synchronization between the systems allows for automatic updates, eliminating manual data entry and reducing the risk of errors. For example, a company using Shopify as its e-commerce platform can integrate its inventory management system to automatically update product availability on the website whenever an order is placed or inventory levels change. This integration streamlines the entire order fulfillment process, from order placement to shipping.
Mobile Inventory Management Applications
Mobile inventory management applications extend the capabilities of inventory systems to handheld devices. These applications typically offer features such as barcode scanning, real-time inventory tracking, order management, and reporting functionalities, enabling employees to perform inventory tasks directly on the warehouse floor or sales floor. The benefits include increased efficiency, reduced errors, and improved data accuracy. For example, a warehouse worker can use a mobile app to scan barcodes as they receive shipments, immediately updating inventory levels and identifying any discrepancies. This real-time data capture eliminates the need for manual data entry and significantly speeds up the receiving process. Moreover, the ability to access real-time inventory data from anywhere allows for better decision-making and improved responsiveness to changing demands.
Security and Data Management
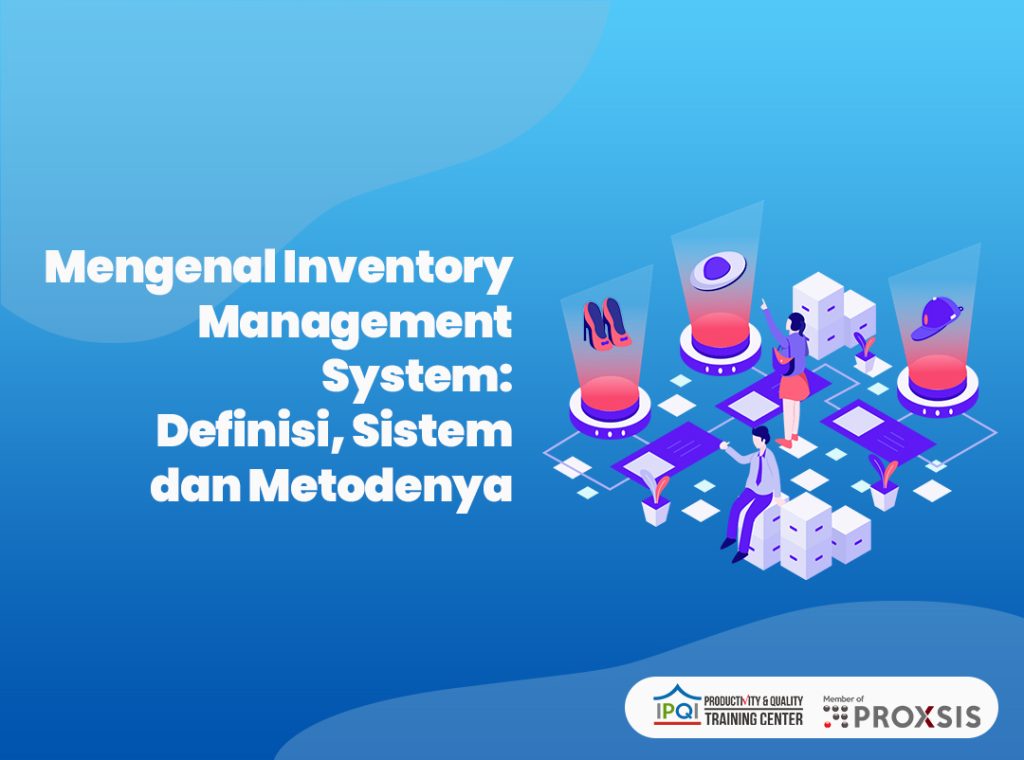
Robust security and efficient data management are paramount for any inventory management system. A compromised system can lead to significant financial losses, operational disruptions, and reputational damage. Therefore, a multi-layered approach encompassing preventative measures, proactive monitoring, and robust recovery plans is crucial.
Potential Security Risks and Mitigation Strategies
Inventory management systems, like any software application storing sensitive data, face various security threats. These include unauthorized access, data breaches, malware infections, and system failures. Effective mitigation strategies involve implementing strong access controls, utilizing encryption for sensitive data both in transit and at rest, regularly updating software to patch vulnerabilities, and employing robust intrusion detection and prevention systems. For instance, multi-factor authentication can significantly reduce the risk of unauthorized access, while regular security audits can identify and address potential weaknesses before they are exploited. Data encryption ensures that even if a breach occurs, the stolen data remains unreadable without the decryption key.
Data Backup and Disaster Recovery Planning
Data loss due to hardware failure, natural disasters, or cyberattacks can severely impact business operations. A comprehensive data backup and disaster recovery plan is essential to minimize downtime and data loss. This plan should include regular backups of the entire inventory database, stored in a geographically separate location, ideally using a cloud-based solution. The plan should also detail procedures for restoring the system in the event of a disaster, including testing the restoration process regularly to ensure its effectiveness. For example, a company might back up its data daily to an offsite server and conduct a full system recovery test quarterly.
Ensuring Data Accuracy and Integrity
Maintaining data accuracy and integrity is crucial for effective inventory management. This requires implementing robust data validation rules, regular data reconciliation processes, and user training on proper data entry procedures. Data validation rules can prevent the entry of incorrect or inconsistent data, while regular reconciliation with physical inventory counts helps identify and correct discrepancies. Employee training should emphasize the importance of accurate data entry and the consequences of errors. For example, the system might automatically flag entries with unrealistic values, such as negative quantities or excessively large orders.
Security Measures Checklist for an Inventory Management System
A comprehensive checklist ensures all critical security measures are in place. This checklist should include:
- Strong password policies and multi-factor authentication
- Regular software updates and patching
- Data encryption (both in transit and at rest)
- Intrusion detection and prevention systems
- Regular security audits and penetration testing
- Comprehensive data backup and disaster recovery plan
- Access control based on the principle of least privilege
- Regular data reconciliation and validation
- Employee training on security best practices
- Incident response plan
Conclusive Thoughts
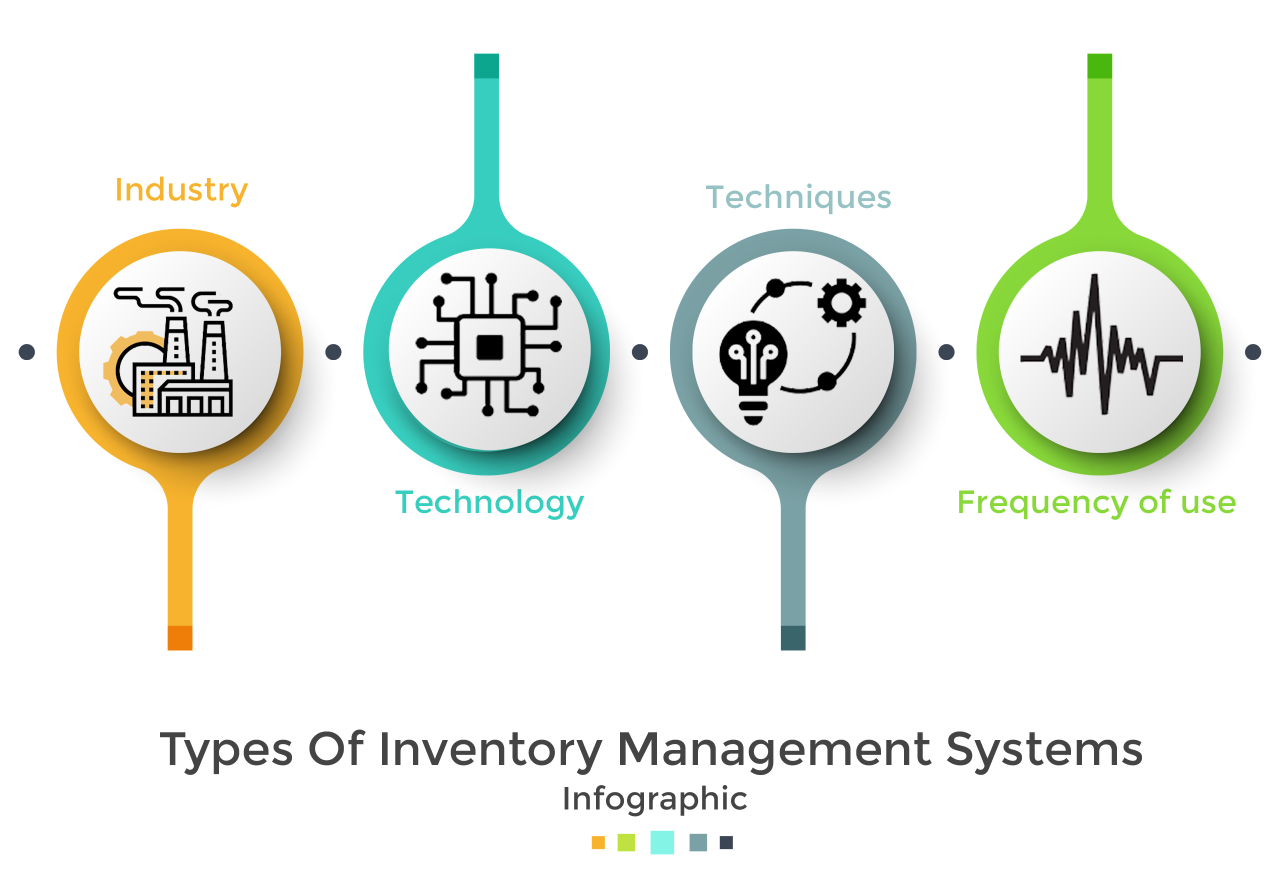
Implementing a robust inventory management system is a strategic investment that yields significant returns. By optimizing inventory levels, improving forecasting accuracy, and leveraging technology, businesses can enhance efficiency, reduce costs, and ultimately drive profitability. This guide has provided a framework for understanding and implementing such a system, empowering businesses to make informed decisions and achieve greater success.